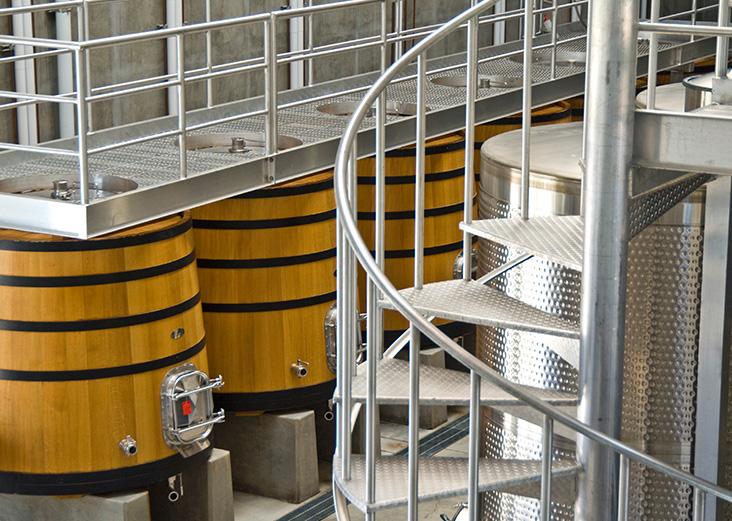
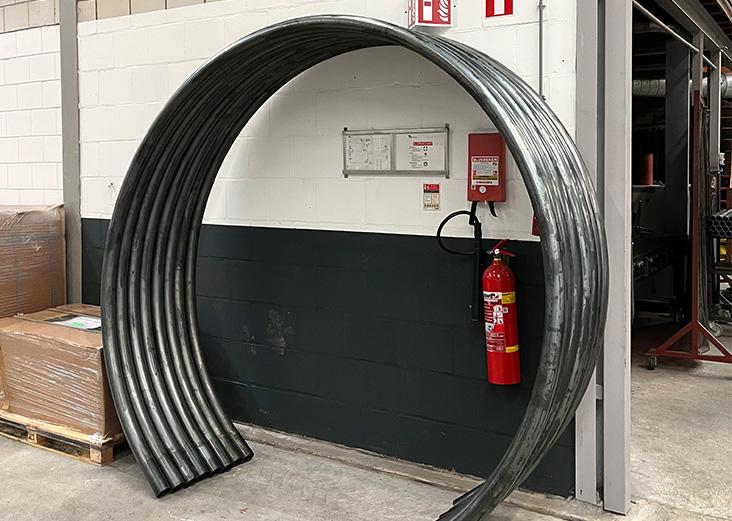
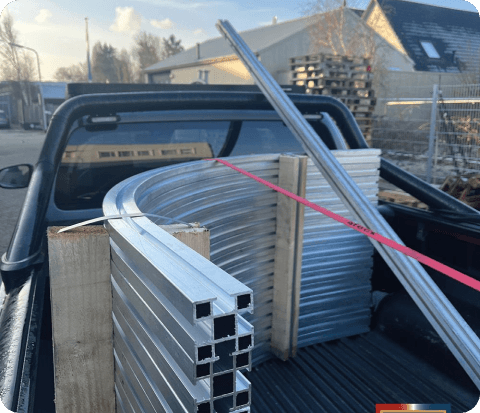
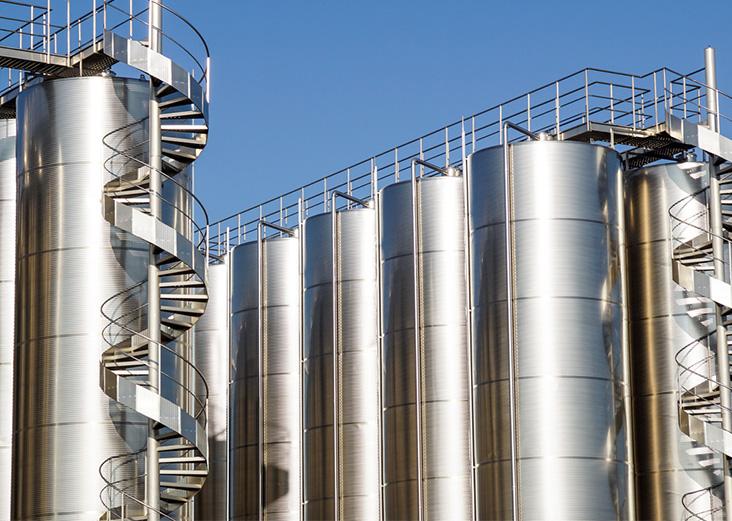
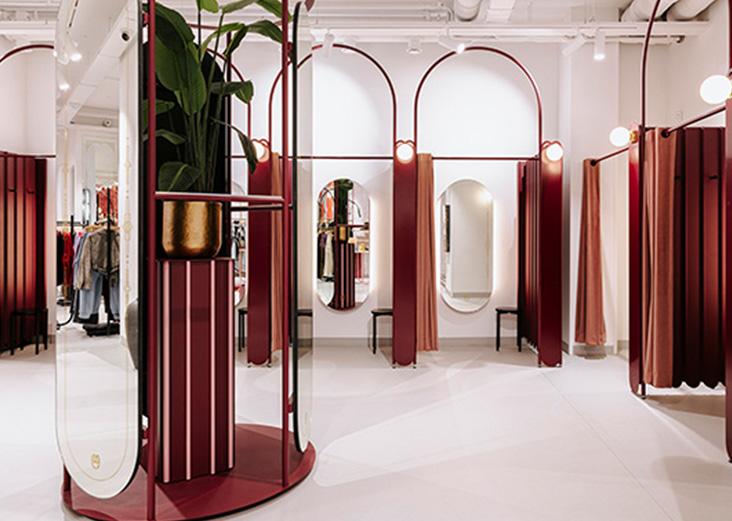
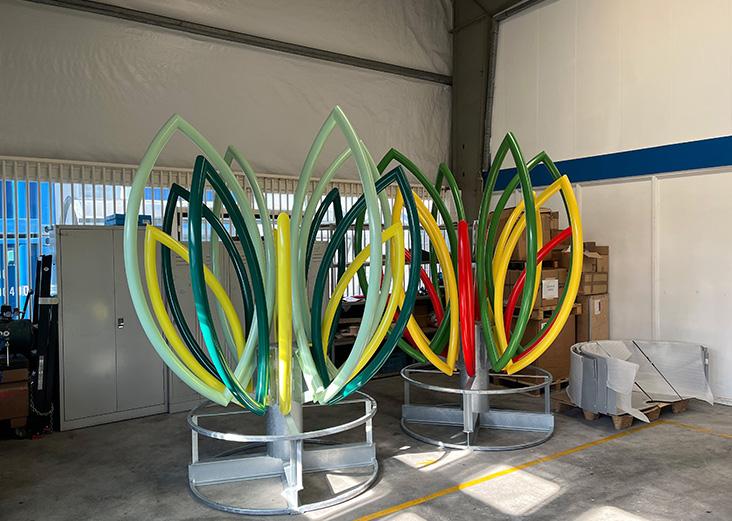
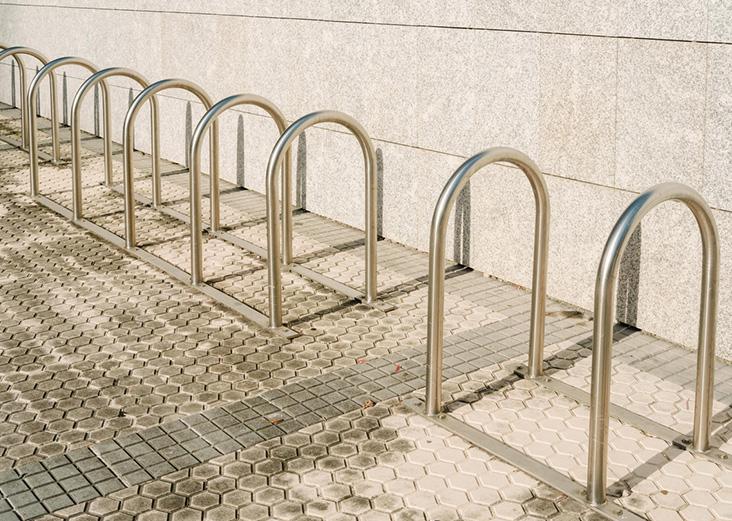
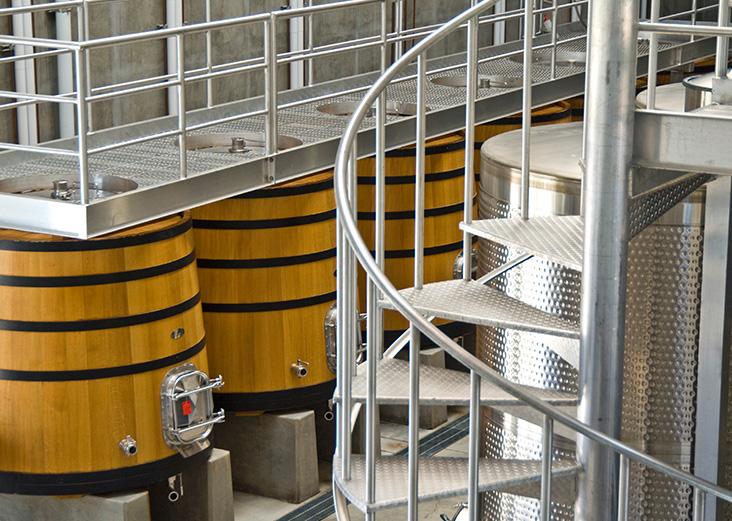
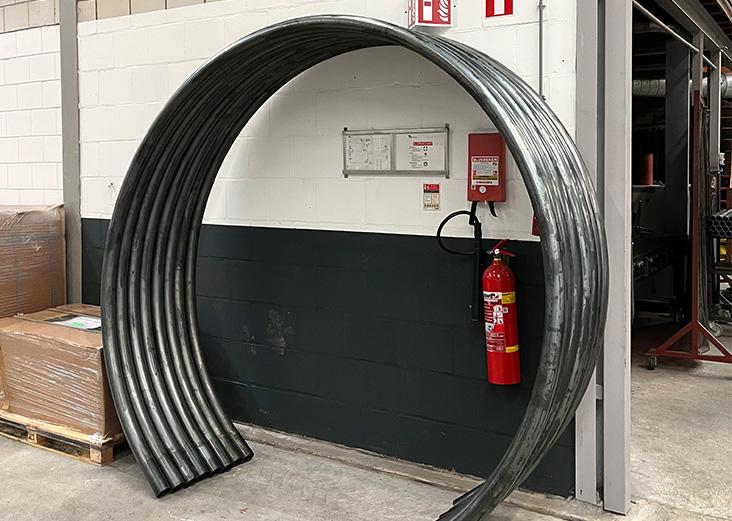
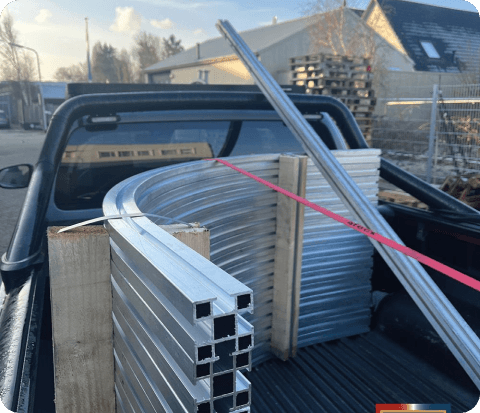
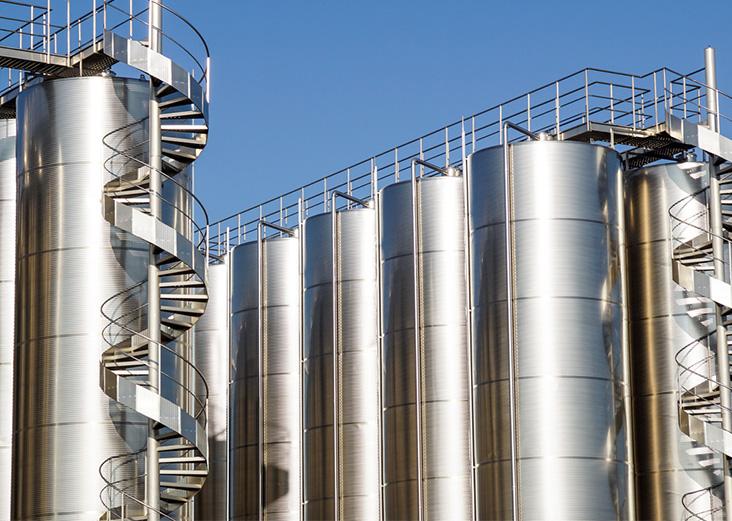
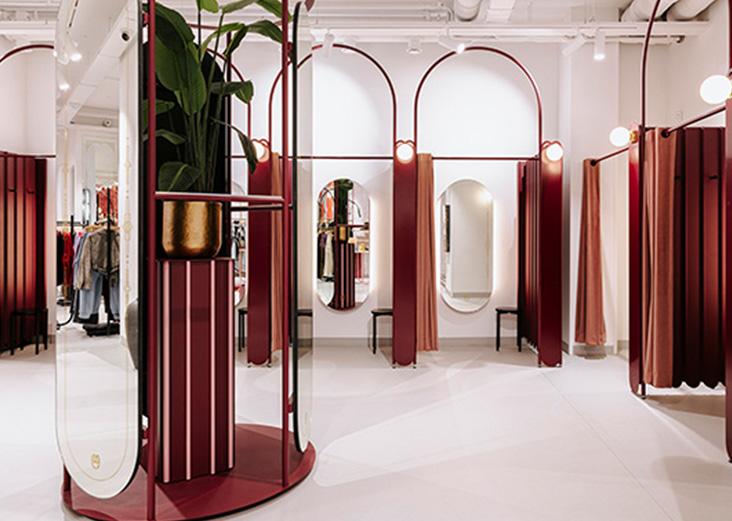
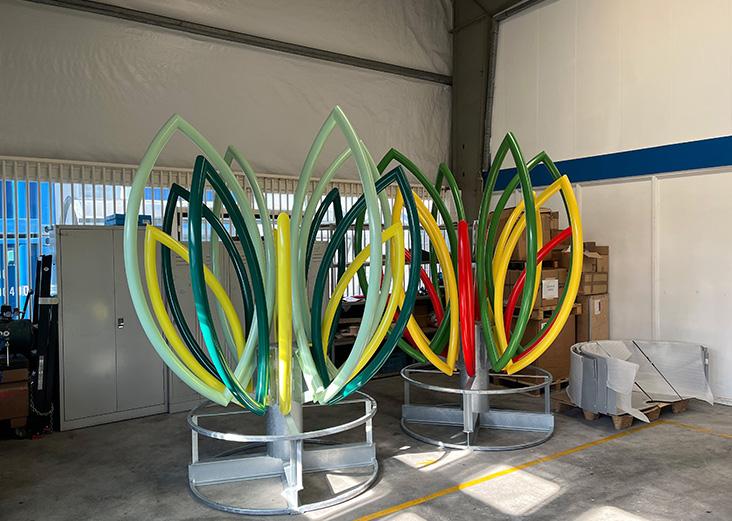
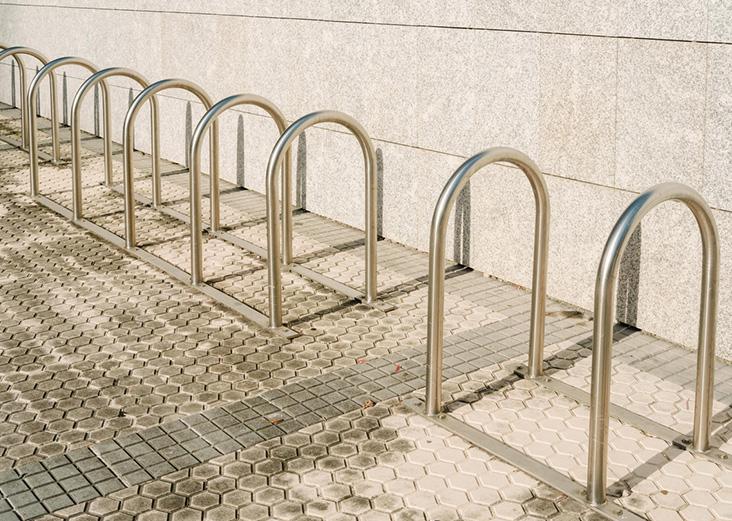
Rolling pipes
Tube rolling can be done with all metals such as aluminum, steel, stainless steel, brass and copper. We use a hydraulic rolling machine for tube rolling with a large radius.
Specifications
Round tubes
16 / 101,6 mm
Square tube
60 / 100 mm
Diamond tube
40 mm
Complete range
Click below
Advantages
Rolling tube profiles

Precision and consistancy
Computer controlled systems ensure precise and repeatable operations, ensuring that each tube profile meets exact specifications and variation between batches is minimal

Efficiency and speed
Automation allows higher production volumes to be achieved in a shorter time, leading to faster lead times and lower production costs.

Quality control
Real time monitoring and adjustments improve product quality, detect defects early and reduce the likelihood of human error.

Flexibility and adjustments
Experience and knowledge of equipment and machinery allow us to quickly switch between different production specifications contributing to a flexible and responsive production environment.

Customer cases
The success story of Nacra Sailing
Nacra Sailing manufactures catamarans for pleasure and racing boats. An innovative company that continuously seeks perfection. One of its innovations is deforming aluminium tube profiles to perfection. Nacra Sailing was looking for a Dutch company capable of thinking along with them, solution-oriented and able to meet their high quality requirements. They found their partner in Buigmeesters. Short lines, fast switching, thinking along with them that is what they certainly appreciate about us.
FAQs
Frequently Asked Questions
Good question!
The mandrel bending and rolling of tube sections are both methods of forming tubes, but they differ in technique and areas of application.
MANDREL BENDING OF TUBE SECTIONS
- In mandrel bending, a tube is bent around a curved jig (or mandrel) to create a precise bend with a specific radius.
- A mandrel, often a long, flexible rod, is inserted into the tube to provide internal support and prevent buckling or deformation of the tube during bending.
- This method uses a bending machine that forces the tube along the mandrel and bending jig to obtain the desired bend.
Applications
- Mandrel bending is ideal for making precise, tight bends with a small radius without deformation of the pipe wall.
- Commonly used in the automotive industry for exhaust systems, roll cages, and hydraulic pipes.
- Also used in furniture manufacturing and HVAC (heating, ventilation and air conditioning) systems where precise bends are required.
Advantages
- High precision and control of bending radius.
- Suitable for complex bended products in 3D
- Suitable for thin-walled pipes and complex bends.
- Minimum distortion and preservation of pipe diameter due to internal mandrel support.
ROLLING OF TUBE SECTIONS
Technology
- Rolling of tube sections, also known as roll bending, uses a series of rollers to gradually bend the tube to the desired shape.
- The tube is passed through the rollers and put under pressure to gradually apply the bend, leading to a smooth curvature.
- This process may require several passes to achieve the final shape, depending on the desired curvature and material strength.
Applications
- Rolling is suitable for forming larger radii and longer bends.
- Often used in construction for making structural elements such as arches and frames, as well as in the production of large pipes and tanks.
- Applied in infrastructure projects such as bridges and railways.
Advantages
- Suitable for larger and thicker pipes.
- Unlimited tube length
- Can create long, smooth bends and complex shapes.
- Less risk of breakage or kinking as the pipe is formed gradually.
COMPARISON
Precision
- Mandrel bending offers higher precision for tight bends with small radii, while rolling is better suited for large, smooth bends.
Applications
- Mandrel bending is ideal for finer, more detailed applications, while rolling is better for structural and large-scale shapes.
Tubes
- Mandrel bending is usually suitable for thin-walled tubes, while rolling works better with thicker and larger tubes.
Distortion
- Mandrel bending prevents distortion thanks to internal support, while rolling relies on gradual pressure to minimise distortion.
Both techniques have their specific advantages and applications, depending on the requirements of the project and the properties of the tubes used.
Good question!
In the automotive industry, rolled tube sections are used because of their lightweight properties combined with high strength, contributing to fuel efficiency and safety. They are used in roll cages, chassis, and exhaust systems because of their precision, consistent quality, and ability for mass production.
Good question!
Furniture manufacturers often choose rolled tubular profiles because of their aesthetic and functional benefits. They offer a clean, modern look and can be produced in a variety of shapes and finishes. In addition, they are durable, lightweight and easy to assemble, which is ideal for mass-produced furniture such as chairs, tables and shelves.
Good question!
For pipeline and energy infrastructure, rolled pipe sections offer advantages such as high resistance to pressure and corrosion, which is essential for transporting oil, gas and other liquids. They are also cost-effective for long-distance transportation and can be manufactured in long lengths without welds, which increases pipeline integrity.
Goede vraag!
To see if we can manufacture your request, you can download our bending & rolling capacity table here. And at the same time, we are happy to think along with you if your profile is not listed. We will work it out together so that you can still receive help.
Do you have a question?
Feel free to contact. Together we love to brainstorm to find the best possible solutions to your request
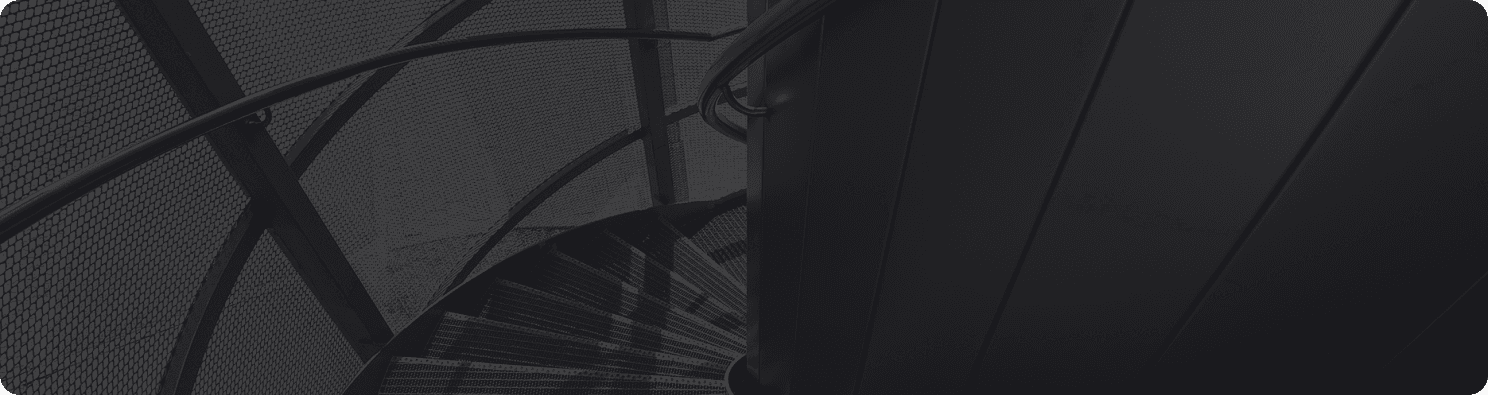
Care to know more about our rolling possibilities?
Ask our team your question? We love to brainstorm with you for the best possible solution
What do our customers say?
WHAT CUSTOMERS SAY ABOUT US