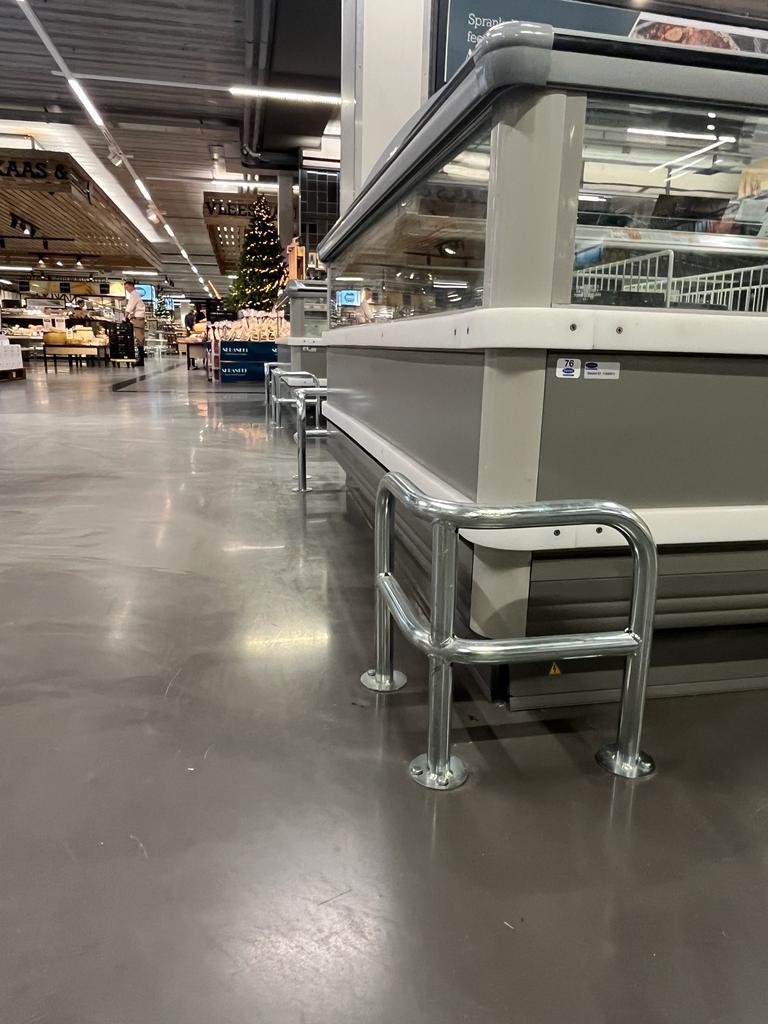
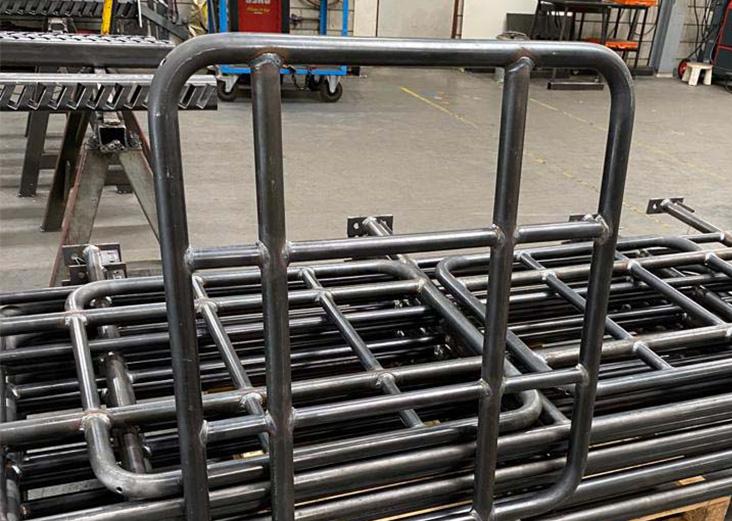
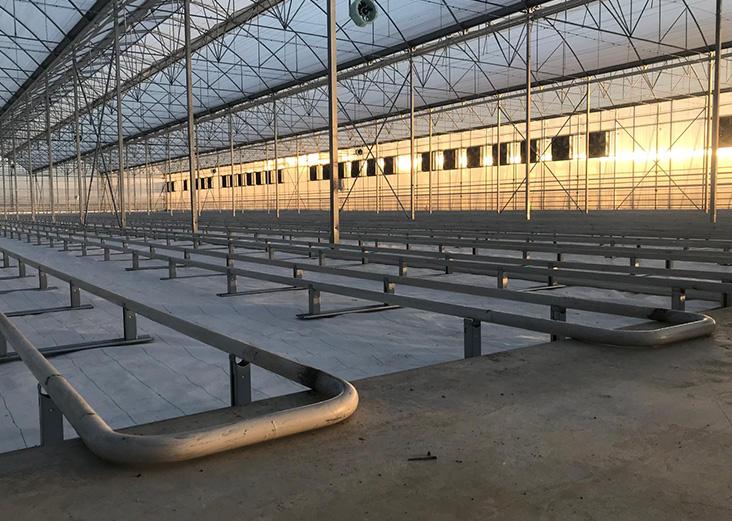
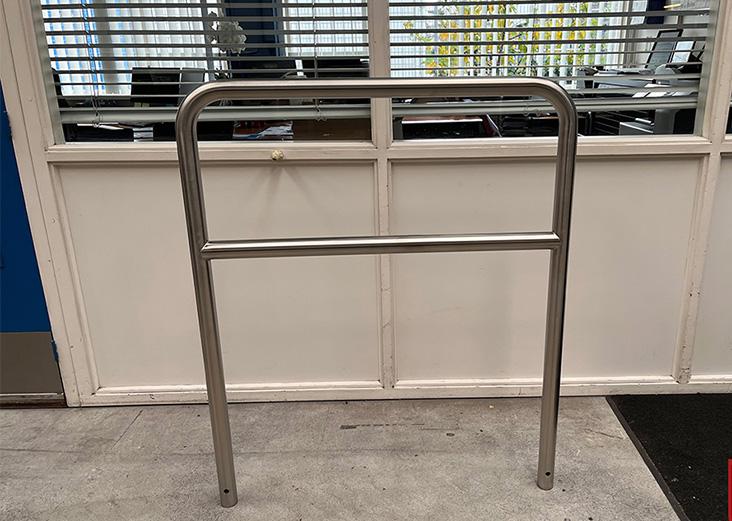
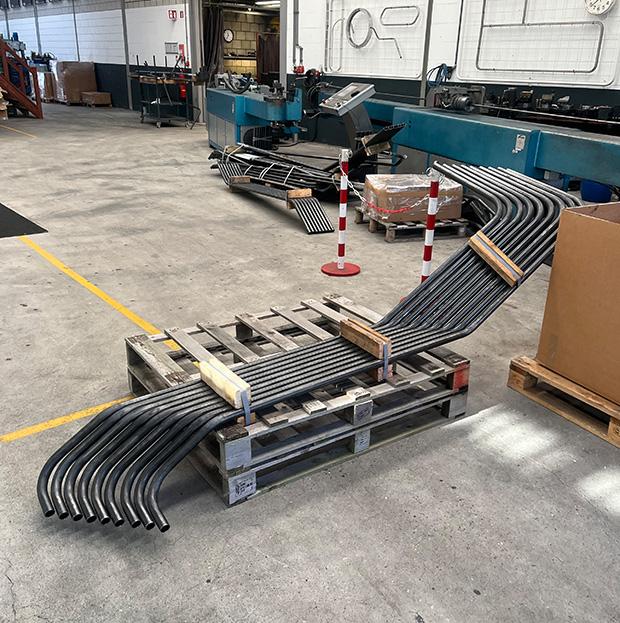
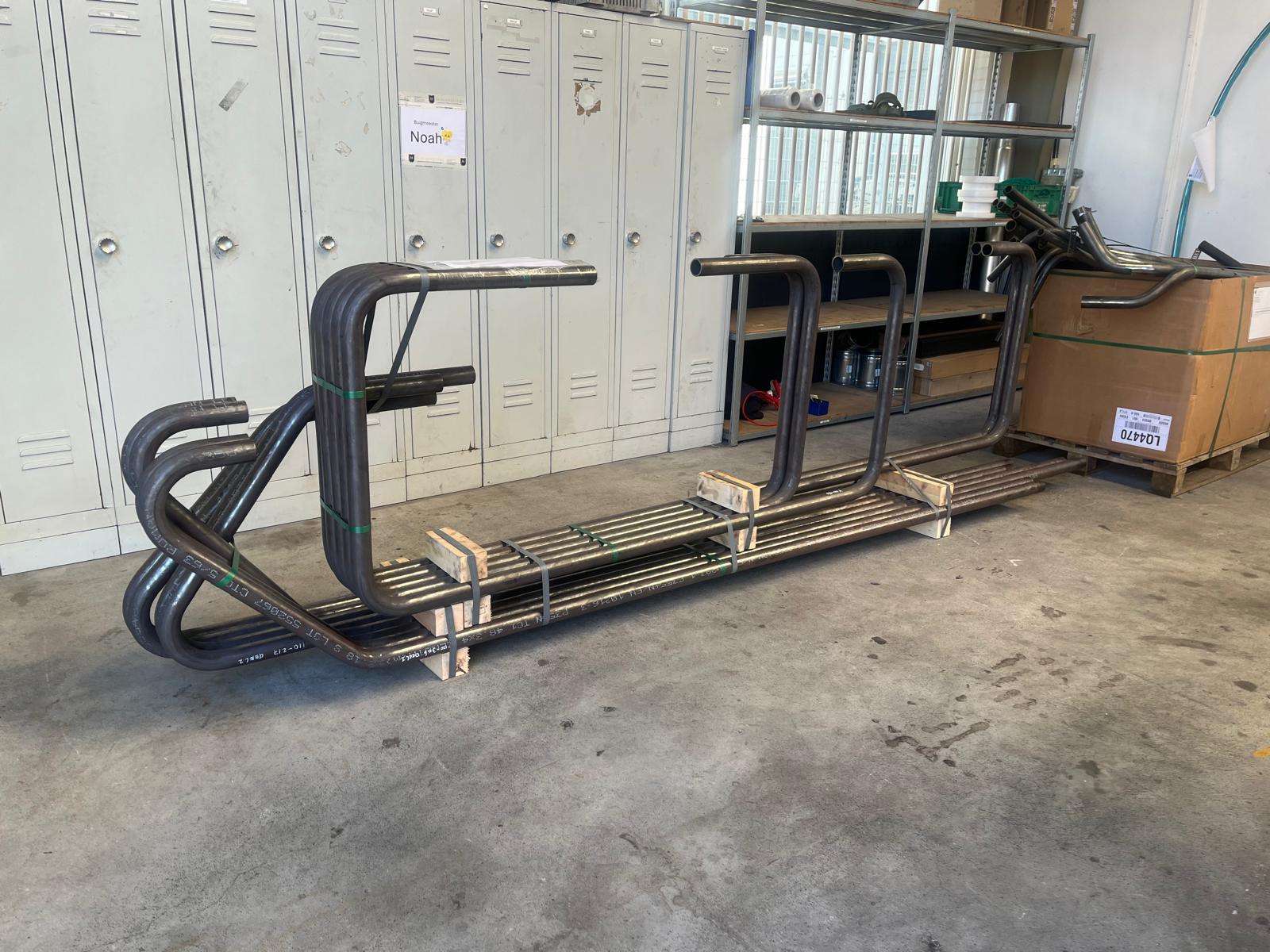

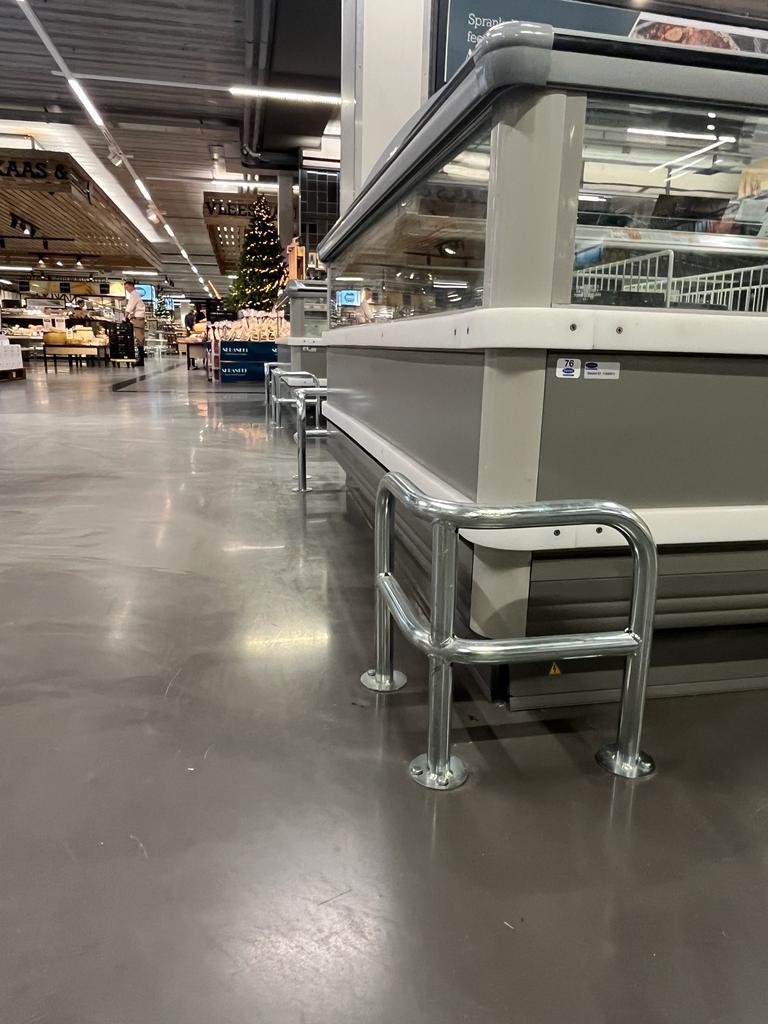
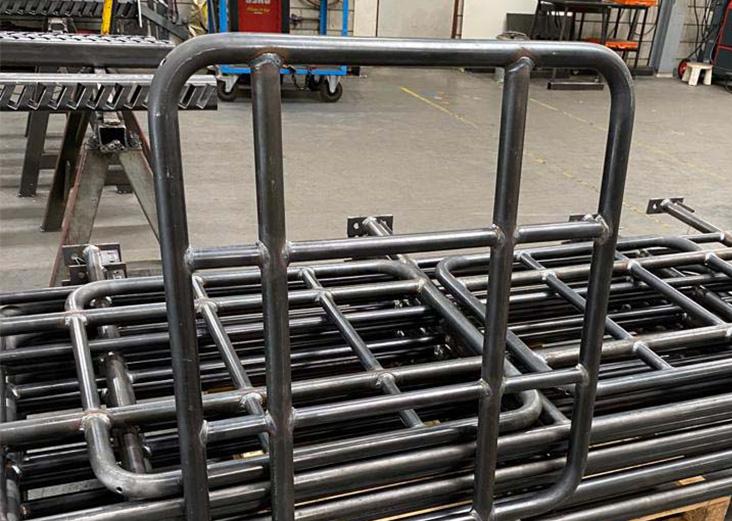
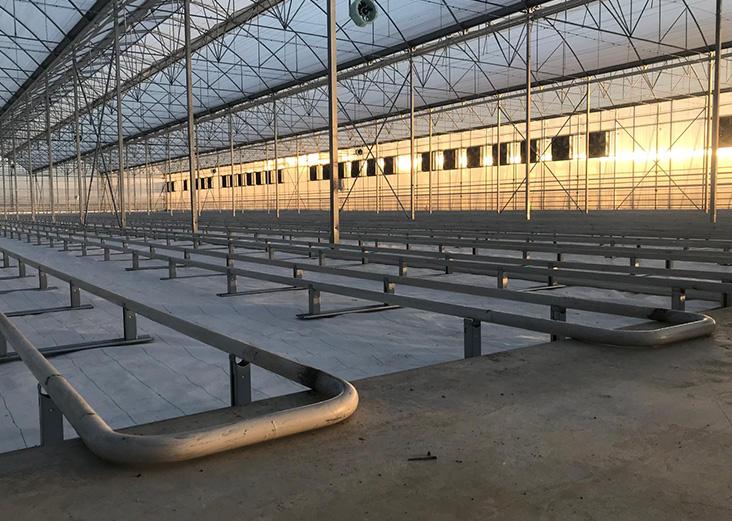
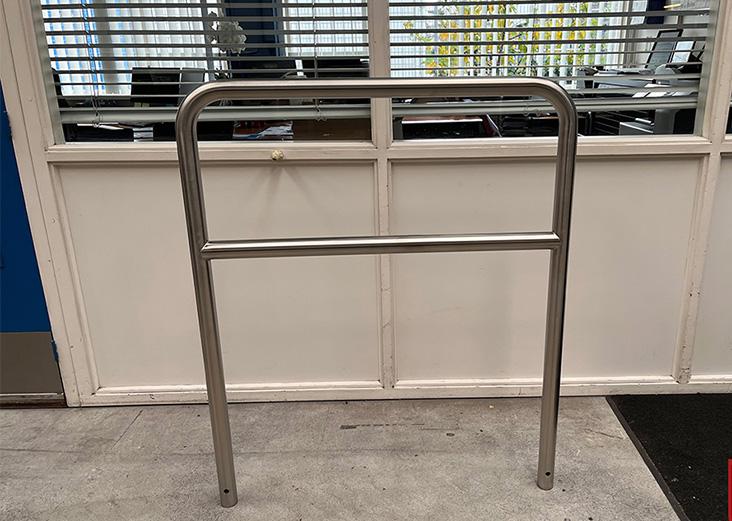
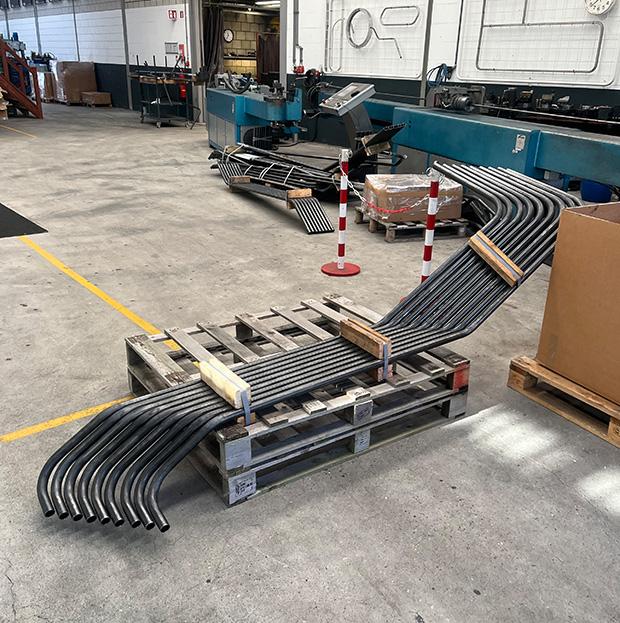
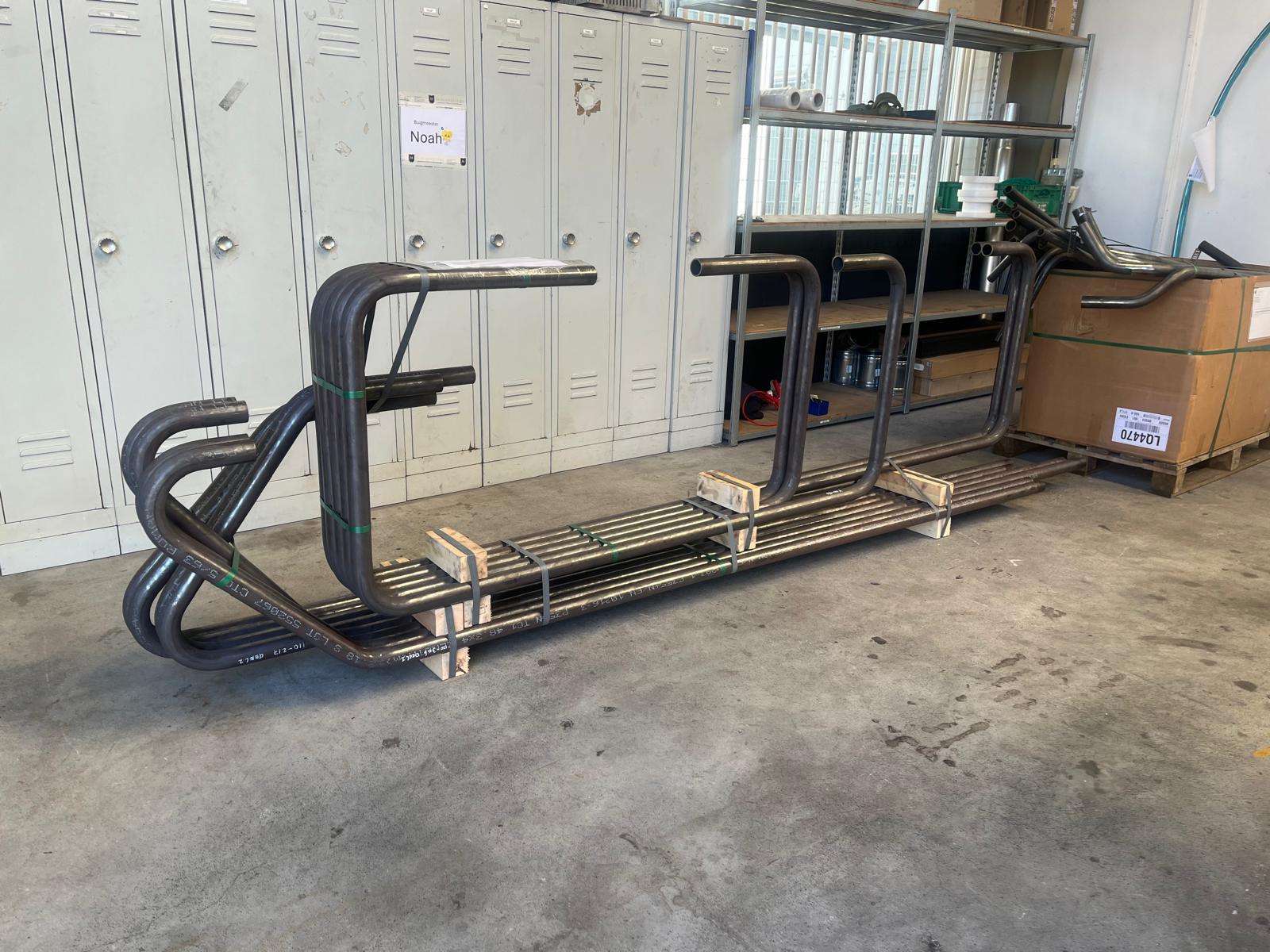

Tube mandrel bending
Are you looking for a proactive partner specialising in the forming of metal tubular profiles?
Deforming steel tube sections is an essential process in various industrial applications, such as in the automotive, horticultural, maritime and construction sectors. One of the most common methods for precise bending of steel tubes is the use of a mandrel.
Below you can see the range we can bend for you.
Round tube diameter
12 t/m 60,3
Square diameter
20 / 40
Complete range
Click download
Technique of deforming steel
Bending metal tube pipes
Principle of mandrel bending
Mandrel bending is a method in which an internal support, the mandrel, is inserted into the pipe to preserve the internal structure during the bending process. This technique is particularly useful for preventing deformations such as oval deformations and wrinkling on the inside of the bend. The mandrel ensures that the tube retains its round shape even on tight bends. Setting up a mandrel bending process can be complex and requires experienced operators to ensure accurate results.
Advantages of mandrel bending
- Precision: Mandrel bending ensures high accuracy and consistency, even on complex bends.
- Quality: Reduces the risk of deformation and wrinkling, resulting in a smoother end product.
- Strength maintenance: Internal support maintains the structural integrity of the tube.
Work process
Cost efficient production

Material saving
By bending tubes instead of welding several straight pieces together, the material is used more efficiently, resulting in less waste and lower material costs.
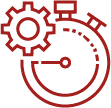
Less labour costs
Tube bending is done on advanced CNC-controlled machines. This speeds up production time, allowing more products to be produced in less time and thus reducing labour costs

Fewer operations
Tube bending eliminates the need for additional processing steps such as welding, grinding and post-processing. This reduces production time and saves on additional processing costs.

Quality and consistancy
The use of specialised bending machines ensures precision and consistency in products. Reduces the likelihood of errors and defects, which in turn leads to fewer rejected products and repairs.
FAQs
Frequently Asked Questions
Good question!
And the clear and short answer is: Download our bending & rolling capacity table here. Is your desired radii not listed? Contact us and we will be happy to think with you how we can still help you.
Good question!
And the clear and short answer is: Download our bending & rolling capacity table here. Is your desired radii not listed? Contact us and we will be happy to think with you how we can still help you.
Good question!
The maximum length for mandrel bending is 6 meter
Good question!
Tolerances may change. In smaller sizes, it’s plus and minus 2 mm. And with the larger sizes, it is a bit larger. This has to do with material type and diameter.
Good question!
Tubes will not deform or collapse because of the mandrell that goes inside the tube while bending.
Good question!
We strive for a 2 weeks delivery scedule
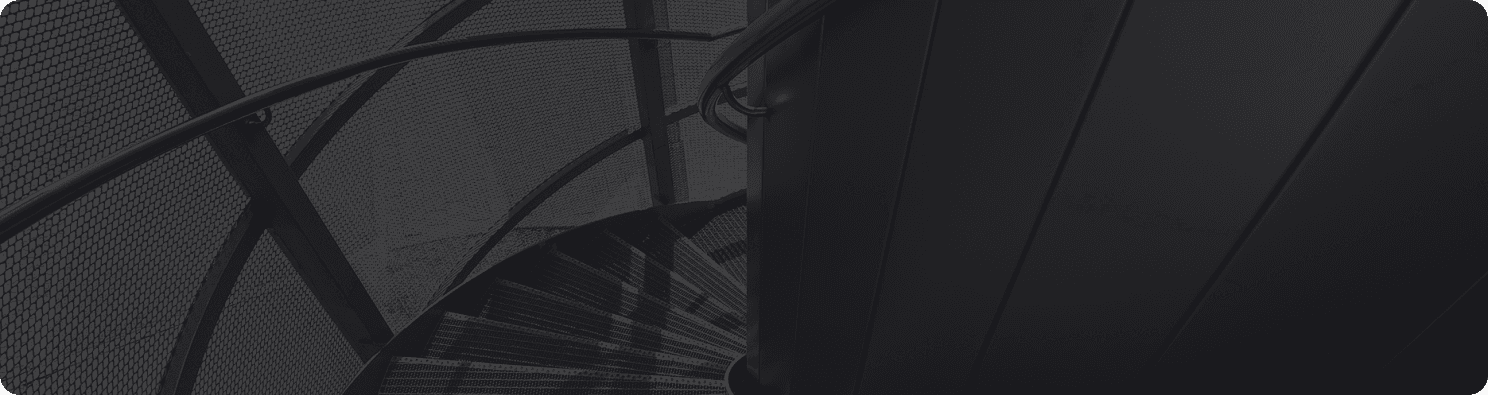
Questions about tube bending?
Contact our bending masters for advice or a visit from our sales manager Theo Stevens
What do our customers say?
WHAT CUSTOMERS SAY ABOUT US